Fabrication
Industrial Training on Fabrication & Welding Technology
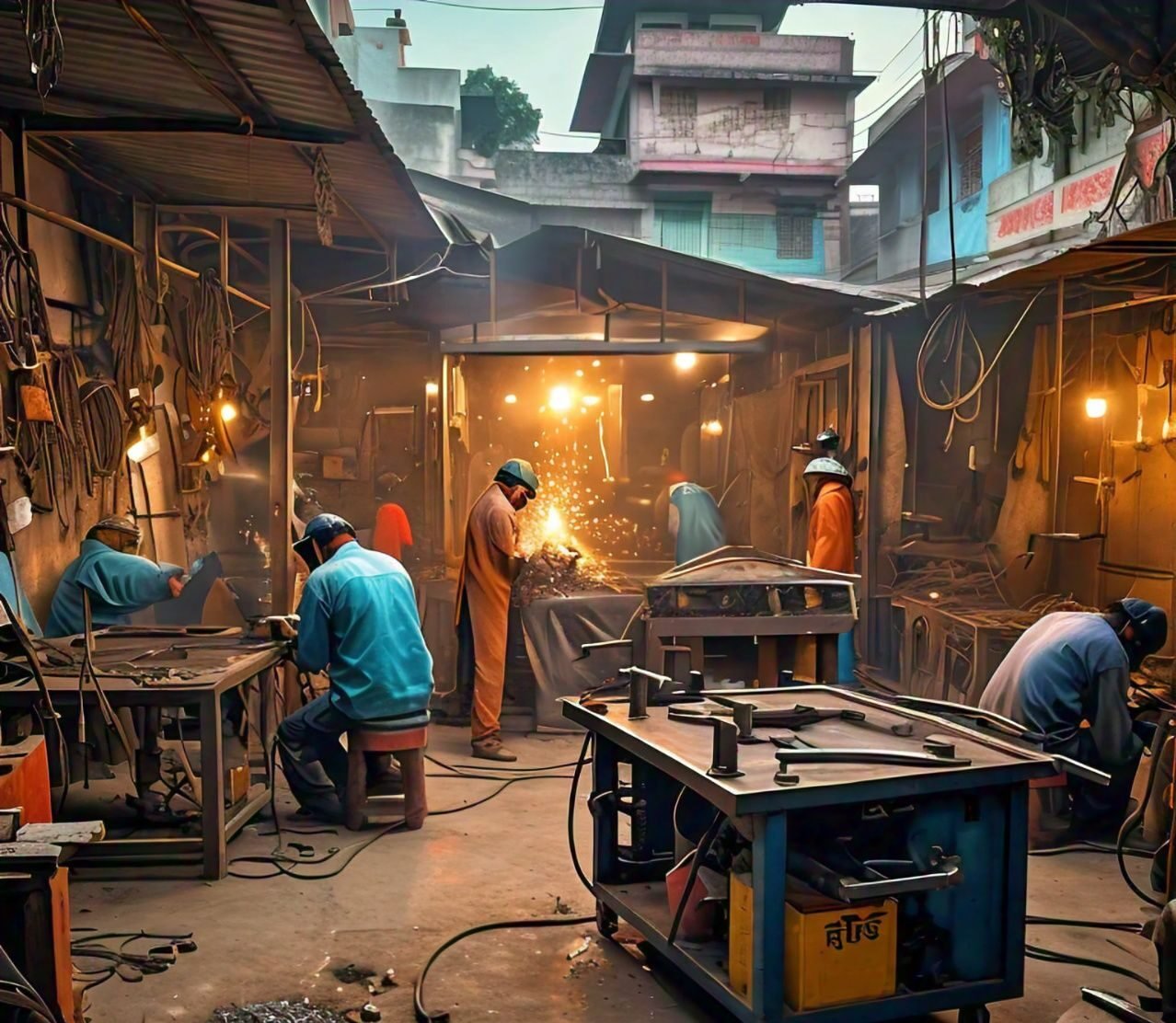
Introduction
The Fabrication and Welding Technology Training Course provides essential skills and knowledge in metalworking, focusing on welding processes, material science, and fabrication techniques. This course is designed for individuals pursuing careers in industries like manufacturing, construction, and automotive, where precision and expertise in welding are crucial. Participants learn various welding methods, such as MIG, TIG, and stick welding, along with cutting, bending, and assembling metal structures. The course emphasizes safety, quality control, and adherence to industry standards, preparing students for successful careers in fabrication and welding.
Curriculum
The Curriculum for Automotive Fabrication & Welding is designed to equip students with the practical skills and technical knowledge needed to work in the automotive industry, focusing on the fabrication and welding of vehicle components. This curriculum covers fundamental welding techniques, advanced fabrication processes, and the application of these skills in automotive repair, modification, and manufacturing.
- Introduction to Automotive Fabrication and Welding
- Overview of Automotive Fabrication
- Role of fabrication in the automotive industry
- Common materials used in automotive fabrication (steel, aluminum, composites)
- Introduction to Welding
- Overview of welding processes: MIG, TIG, Stick, and Spot welding
- Importance of welding in automotive repair and manufacturing
- Safety Practices and Workshop Management
- Workshop Safety Protocols
- Proper use of personal protective equipment (PPE)
- Handling and storage of materials and tools
- Welding Safety
- Safe handling of welding equipment
- Ventilation, fire prevention, and emergency procedures
- Workshop Organization
- Efficient layout and management of fabrication and welding workspaces
- Inventory management and tool maintenance
- Welding Processes and Techniques
- MIG (Metal Inert Gas) Welding
- Principles of MIG welding and its applications in automotive fabrication
- Setting up and operating MIG welding equipment
- Welding techniques for various automotive components
- TIG (Tungsten Inert Gas) Welding
- Fundamentals of TIG welding, especially for aluminum and stainless steel
- Precision welding for automotive parts requiring high strength and aesthetics
- TIG welding for thin materials and complex shapes
- Stick Welding (SMAW)
- Basics of Stick welding for heavy-duty automotive applications
- Advantages and limitations of Stick welding in automotive repair
- Techniques for welding thicker sections and under harsh conditions
- Spot Welding
- Overview of spot welding in automotive assembly
- Applications in joining sheet metal and body panels
- Use of spot welders in repair and manufacturing
- Automotive Fabrication Techniques
- Sheet Metal Fabrication
- Basics of working with sheet metal: cutting, bending, and shaping
- Tools and techniques for fabricating automotive body panels
- Joining methods: riveting, bolting, and welding
- Tube and Pipe Fabrication
- Fabrication of roll cages, exhaust systems, and frames
- Techniques for bending, cutting, and welding tubes and pipes
- Stress analysis and reinforcement for safety-critical components
- Chassis Fabrication and Repair
- Fundamentals of chassis design and fabrication
- Techniques for repairing and reinforcing automotive chassis
- Alignment and measurement tools for chassis fabrication
- Custom Fabrication and Modifications
- Fabricating custom parts for vehicle modification and restoration
- Techniques for integrating new components into existing structures
- Working with aftermarket parts and custom fabrication requests
- Material Science for Welding and Fabrication
- Metallurgy Basics
- Properties of metals commonly used in automotive fabrication (steel, aluminum, alloys)
- Heat treatment processes and their effects on metal properties
- Material selection for strength, weight, and corrosion resistance
- Welding Metallurgy
- Understanding the effects of welding on metal structures
- Common welding defects (cracking, warping, porosity) and how to prevent them
- Techniques for post-weld treatment and stress relief
- Advanced Materials
- Working with advanced materials like high-strength steels and composites
- Challenges and techniques for welding advanced materials
- Applications of advanced materials in modern automotive design
- Automotive Body Repair and Fabrication
- Body Panel Fabrication and Repair
- Techniques for repairing damaged body panels
- Fabricating replacement panels from scratch
- Techniques for aligning and installing panels
- Frame Straightening and Repair
- Methods for assessing and repairing damaged vehicle frames
- Use of frame alignment tools and techniques
- Reinforcing and modifying frames for performance and safety
- Restoration of Classic Cars
- Techniques for fabricating parts for vintage and classic vehicles
- Challenges in working with older materials and designs
- Custom fabrication for restoration projects
- Welding Certification Preparation
- Welding Standards and Certifications
- Overview of industry standards and certifications (e.g., AWS, ASME)
- Preparation for welding certification tests
- Practice exams and assessment of welding skills
- Practical Welding Exams
- Hands-on testing of welding skills in a controlled environment
- Certification in specific welding processes (MIG, TIG, Stick)
- Continuous Skill Development
- Techniques for improving and refining welding skills
- Staying updated with the latest welding technologies and standards
- CAD and CNC for Fabrication
- Introduction to CAD (Computer-Aided Design)
- Basics of CAD software for designing automotive parts
- Creating 2D drawings and 3D models for fabrication projects
- Converting designs into fabrication-ready blueprints
- CNC (Computer Numerical Control) Machining
- Basics of CNC machines and their role in automotive fabrication
- Programming CNC machines for cutting, shaping, and drilling
- Integrating CNC machining with manual fabrication techniques
- CAM (Computer-Aided Manufacturing)
- Using CAM software to plan and execute fabrication processes
- Simulation and verification of CNC machining processes
- Optimization of tool paths and material usage
- Quality Control and Inspection
- Inspection Techniques
- Visual inspection of welds and fabricated components
- Use of tools like calipers, micrometers, and gauges for precision measurement
- Nondestructive testing (NDT) methods: ultrasonic, radiographic, and dye penetrant
- Quality Assurance in Fabrication
- Establishing quality control procedures in a fabrication workshop
- Documentation and reporting of quality control checks
- Continuous improvement practices for maintaining high standards
- Defect Analysis and Remediation
- Identifying common defects in welds and fabricated parts
- Techniques for repairing and preventing defects
- Root cause analysis and corrective actions in the fabrication process
- Hands-On Projects and Workshops
- Practical Welding Projects
- Completing welding projects that simulate real-world automotive repairs and modifications
- Projects involving different materials, thicknesses, and joint configurations
- Collaborative projects that require teamwork and problem-solving
- Fabrication Workshops
- Building custom automotive components from design to completion
- Workshops on specific fabrication techniques like tube bending, panel beating, and chassis reinforcement
- Real-world projects, such as restoring a vehicle or building a custom car part
- Capstone Project
- A comprehensive project that involves both welding and fabrication skills
- Designing, fabricating, and assembling a complex automotive component or structure
- Presenting the project, including design rationale, fabrication process, and quality assurance
- Industry Engagement and Internship
- Industry Visits
- Tours of automotive manufacturing plants and fabrication workshops
- Observation of advanced welding and fabrication techniques in a professional setting
- Networking opportunities with industry professionals
- Guest Lectures
- Sessions with experienced welders, fabricators, and automotive engineers
- Insights into current industry trends, challenges, and innovations
- Internship Opportunities
- Practical experience in an automotive workshop or manufacturing environment
- Applying learned skills in a real-world setting under professional supervision
- Gaining exposure to the day-to-day operations of automotive fabrication and welding
- Final Assessment and Certification
- Practical Exams
- Evaluation of welding and fabrication skills through hands-on testing
- Assessment of precision, technique, and adherence to safety protocols
- Theory Exams
- Testing knowledge of material properties, welding processes, and fabrication techniques
- Assessment of understanding of industry standards and best practices
- Certification
- Awarding of certification upon successful completion of the course, recognizing proficiency in automotive fabrication and welding
This curriculum is designed to provide students with a solid foundation in automotive fabrication and welding, preparing them for careers in the automotive industry, whether in manufacturing, repair, or custom vehicle modification.
The Curriculum for Structural Fabrication and Welding is tailored to provide in-depth knowledge and practical skills required for fabricating and welding structural components. This curriculum is essential for those looking to work in industries such as construction, manufacturing, and infrastructure development, where structural integrity and precision are critical.
Introduction to Structural Fabrication and Welding
- Overview of Structural Fabrication
- Importance of structural fabrication in construction and industry
- Common structures: bridges, buildings, pipelines, and industrial frameworks
- Introduction to Welding in Structural Fabrication
- Role of welding in creating and maintaining structural integrity
- Types of welding processes used in structural fabrication (MIG, TIG, Stick)
- Basics of structural design and load-bearing considerations
Safety Practices in Structural Welding and Fabrication
- Workshop Safety Protocols
- Importance of personal protective equipment (PPE) in structural welding
- Handling and storage of heavy materials and equipment
- Welding Safety
- Safe operation of welding machines and handling of high-voltage equipment
- Fire prevention, ventilation, and emergency response procedures
- Site Safety for Structural Fabrication
- Working at heights: safety harnesses, scaffolding, and ladders
- Heavy lifting techniques and use of cranes or other lifting equipment
Welding Processes and Techniques for Structural Applications
- MIG Welding (Metal Inert Gas)
- Principles of MIG welding in structural steel fabrication
- Techniques for welding thick materials and large structural components
- Advantages and applications of MIG welding in construction
- TIG Welding (Tungsten Inert Gas)
- Precision welding techniques for critical structural joints
- Welding non-ferrous metals like aluminum and stainless steel in structural applications
- Use of TIG welding for aesthetic and high-strength structural welds
- Stick Welding (SMAW)
- Basics of Stick welding for heavy-duty structural applications
- Techniques for welding in various positions (vertical, overhead, etc.)
- Stick welding in harsh environments and remote locations
- Submerged Arc Welding (SAW)
- Overview of SAW for high-productivity structural welding
- Application of SAW in welding large beams, columns, and girders
- Advantages of SAW for welding thick sections with high deposition rates
Structural Fabrication Techniques
- Cutting and Shaping Structural Materials
- Techniques for cutting steel plates, beams, and pipes (oxy-fuel cutting, plasma cutting)
- Bending and shaping techniques for structural components
- Introduction to CNC cutting machines for precision fabrication
- Assembly of Structural Components
- Techniques for aligning and fitting structural members
- Use of jigs and fixtures to ensure precision during assembly
- Tack welding and temporary fastening methods
- Welding Structural Joints
- Types of joints used in structural fabrication: butt, lap, and corner joints
- Techniques for welding different joint configurations in structural components
- Pre-heating and post-weld treatment to prevent cracking and distortion
- Heavy Structural Fabrication
- Fabrication of large and complex structures like bridges, towers, and industrial frameworks
- Use of cranes and rigging equipment for assembling large components
- Techniques for ensuring structural integrity during and after fabrication
Material Science for Structural Welding
- Metallurgy Basics for Structural Applications
- Properties of structural steels and alloys
- Heat treatment and its effects on structural metals
- Material selection based on strength, ductility, and environmental factors
- Welding Metallurgy
- Effects of welding on the microstructure of structural metals
- Common welding defects (cracking, porosity, distortion) and prevention methods
- Understanding the heat-affected zone (HAZ) in structural welding
- Advanced Materials in Structural Fabrication
- High-strength steels and their applications in modern structures
- Welding techniques for advanced materials like weathering steel and duplex stainless steel
- Considerations for welding dissimilar metals in structural fabrication
Structural Design and Engineering Principles
- Basic Structural Engineering Concepts
- Understanding loads, stresses, and strains in structures
- Load-bearing principles and distribution in different types of structures
- Introduction to structural analysis and design software
- Design of Welded Structures
- Designing joints and welds for maximum strength and durability
- Standards and codes for structural welding (e.g., AWS D1.1)
- Importance of weld size, length, and placement in structural integrity
- Blueprint Reading and Interpretation
- Understanding and interpreting structural blueprints and welding symbols
- Translating design specifications into practical fabrication steps
- Use of CAD drawings in structural fabrication projects
Quality Control and Inspection in Structural Welding
- Inspection Techniques
- Visual inspection of welds and structural assemblies
- Use of non-destructive testing (NDT) methods: ultrasonic, radiographic, magnetic particle, and dye penetrant testing
- Dimensional inspection and tolerance checking for structural components
- Welding Codes and Standards
- Overview of industry standards for structural welding (AWS, ASME, ISO)
- Compliance with national and international codes for structural fabrication
- Documentation and record-keeping for quality assurance in welding
- Defect Analysis and Remediation
- Identification and correction of welding defects in structural fabrication
- Techniques for repairing defective welds and ensuring structural integrity
- Root cause analysis of welding failures and implementation of corrective actions
Advanced Fabrication Techniques
- Welding Automation in Structural Fabrication
- Introduction to automated welding processes (robotic welding, mechanized welding)
- Applications of welding automation in high-volume structural fabrication
- Programming and operation of welding robots and automated systems
- Modular Fabrication and Prefabrication
- Techniques for fabricating large structural modules off-site
- Benefits of prefabrication in terms of time, cost, and quality
- Challenges and considerations in transporting and assembling prefabricated modules
- Specialized Structural Fabrication Projects
- Fabrication of specialized structures such as tanks, silos, and pressure vessels
- Techniques for working with high-pressure and high-temperature environments
- Fabrication of structures designed for seismic, wind, or other environmental loads
Practical Welding Projects and Workshops
- Hands-On Welding Projects
- Fabrication and welding of structural components like beams, columns, and trusses
- Real-world projects involving the assembly of structural frameworks
- Collaborative projects that simulate construction site conditions
- Fabrication Workshops
- Workshops focused on specific fabrication techniques such as cutting, bending, and joining
- Use of heavy machinery and tools in structural fabrication
- Practical training in aligning and fitting large structural components
- Capstone Project
- Comprehensive project involving the design, fabrication, and assembly of a structural component or framework
- Collaboration with industry partners for real-world application and feedback
- Presentation of the project, including design rationale, fabrication process, and quality assurance measures
Industry Engagement and Internship
- Industry Visits
- Tours of construction sites, steel fabrication shops, and manufacturing plants
- Observation of large-scale structural fabrication and welding projects
- Networking opportunities with industry professionals
- Internship Opportunities
- Practical experience in a structural fabrication workshop or construction site
- Application of learned skills in real-world settings under professional supervision
- Exposure to the day-to-day operations of structural fabrication and welding
Final Assessment and Certification
- Practical Exams
- Evaluation of welding and fabrication skills through hands-on testing
- Assessment of precision, technique, and adherence to safety protocols in structural welding
- Theory Exams
- Testing knowledge of material properties, welding processes, and structural design principles
- Assessment of understanding of industry standards and best practices in structural fabrication
- Certification
- Awarding of certification upon successful completion of the course, recognizing proficiency in structural fabrication and welding
This curriculum is designed to provide students with the necessary skills and knowledge to excel in the field of structural fabrication and welding. It prepares them for careers in construction, manufacturing, and other industries where the fabrication and welding of structural components are essential.